To combat the environmental crisis, carbon gas emissions must be significantly reduced, the solutions implemented so far are not sufficient and more innovative approaches must be adopted. Drastic changes are needed to reach the 85% and 100% decarbonisation targets for the industrial and energy sectors respectively by 2050. Among the solutions that must be implemented are the electrification of industrial processes, the optimization of process yields, as well as the substitution of conventional fuels by low-carbon energy sources.
A promising approach is the coupling of heterogeneous catalysis in continuous with the electrification of industrial processes, and more precisely magnetic induction.
Heterogeneous catalysis is the predominant form of catalysis in the industrial sector and plays an important role in the production of nearly 80% of chemicals. It is generally based on the use of solid catalysts in a gas or liquid reaction environment. The reaction takes place on the catalyst surface where the reagents are adsorbed, and as a result the final product is desorbed to the reaction medium. At the end of the reaction the catalyst can be recovered and reused in a new reaction cycle.
This type of catalysis provides various advantages for industrial processes:
- Increased productivity (faster response, increased selectivity and conversion rates)
- Ease of use (separation and recycling of catalyst)
- Change in operating conditions (decrease in operating temperatures and pressures)
- Environmental benefits (recyclable catalyst, reduction of pollutant, reduction of chemical solvents used).
The majority of heterogeneous catalysis processes are implemented in continuous reactors with fixed or fluidized beds. Fixed bed reactors are the most widespread technology thanks to their simplicity of development and operation. Continuous operations bring a number of advantages over batch processes:
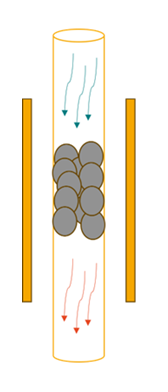
- Continuous flow allows for better online and dynamic control of the process and reaction by controlling key parameters such as residence time and temperature.
- The production flow is flexible, so the processes are customizable to suit different reactions and fluctuations in demand.
- The use of continuous flow reactors limits the amount of reagents in contact and therefore reduces the risk of runaway and explosion in the case of highly exothermic and hazardous reactions.
- Continuous flow reduces the limitations of mass and energy transfers.
The operating principles of the two approaches are highly compatible, a large part of the heterogeneous catalysts used in industrial applications are based on metals or deposited on metals susceptible to magnetic heating. By means of induction the heating would be selective and fast, the catalysts will be targeted and their surface activated selectively and quickly for the chemical reaction. This type of heating will bring energy savings since only the useful part (the catalyst) is heated, as well as gains in productivity, selectivity, control and flexibility of the reactor and reactions.
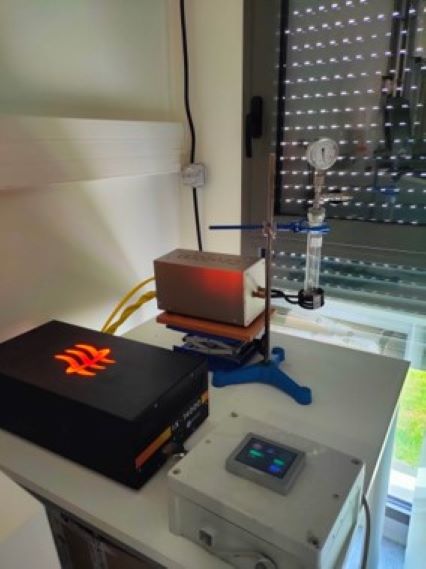
Chemical reactions activated by metal-based catalysts at the industrial level include synthesis methane production reactions (the Sabatier reaction), methanol reforming reaction, methanol synthesis and ammonia synthesis. These reactions are of paramount importance since they provide solutions for energy transition, low-carbon fuels and intermittent energy transport and storage.
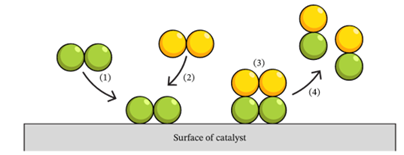
For example, in the case of the methanation reaction, it can be set up after a biogas digester or we will have a biogas composed of 70% biomethane and 30% CO2. The methanation reaction will transform CO2, reacting it with H2 in the presence of metal catalyst, into methane to result in 100% pure and injectable biomethane in the natural gas network. To have a low carbon process renewable energy sources (solar or wind) are used to produce hydrogen by electrolysis. In addition, intermittent renewable energies can be used for magnetic heating due to the speed and flexibility of this type of heating. So we end up with an ecological process that transforms a greenhouse gas into a form of energy that is storable, transportable and low carbon.